

There are a couple questions that can help narrow down the answer. You want to make sure the screen is dry because how dry it is will determine how your emulsion cures. When determining the type of emulsion to use for your screen prints.

Let gravity help you hereby making a thicker stencil for your design.
#Emulsion for screen printing software
Photographs can be manipulated with software in various ways to make a suitable image.
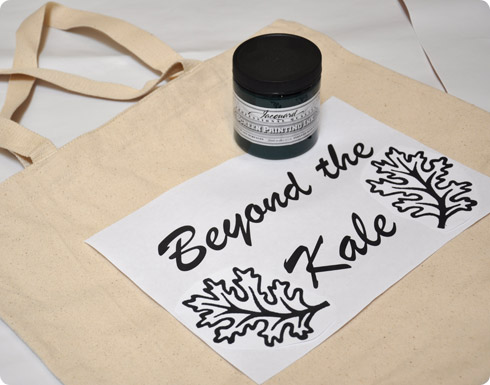
Manufactured by MURAKAMIs original patented PVA/SBQ. The image, however, has to be black and white. MURAKAMI photosensitive emulsions offer the best quality available in screen printing industry. The image can be anything including photographs, drawings, computer-printed text or illustrations anything. Once you’ve identified your dry method above and your screen is coated and degreased, place it horizontally with the print side down to dry. Photo emulsion is light sensitive so we can use light to transfer an image to the screen. Emulsion is a solution used in many printing and photography labs, and can be made at home. These units run anywhere from $2,000 - $5,000 The vellum is then placed onto a silk screen coated with emulsion and set under lighting to burn the design in. Commercial drying cabinets are uncommon, but if you’re lucky enough to have one, the temperature-controlled space helps speed up the drying process. The ideal drying temperature for your coated screen is between 85-95 degrees Fahrenheit with low humidity. Commercial Drying Cabinet – These should max out at around 100 degrees Fahrenheit.We suggest investing in a small, inexpensive fan to circulate airflow inside the cabinet. Your screens will air-dry naturally at room temperature. DIY Drying Cabinet – Most printers will have a screen rack with a cover or a DIY cabinet that is dark and dust-free.Here are two methods that can be used to dry wet emulsion before exposing: A wet screen can cause emulsion to break down prematurely on the press.Wet emulsion will not expose properly, and you will not get a clean crisp image.Why it's critical your emulsion is dry before you start printing:
#Emulsion for screen printing how to
Here we dive into why it’s important, how to do it properly, and how long it takes for screen printing emulsion to dry. Emulsions are available in three basic types: diazo, dual cure, and pure photopolymer. Screen emulsions in accordance with the present invention include a poly vinyl alcohol and poly vinyl acetate or a poly vinyl acetate copolymer emulsified. Once the screen is dry it is ready to be exposed. The emulsion is coated on the screen with a scoop coater or an automatic coater. Did you know that drying your screen once it’s been coated with emulsion is critical to the printing process? It’s a step that’s often overlooked but is so important for a successful print. Screen printing emulsion is essentially a light sensitive glue used for creating a stencil on screen mesh. I think this is very important because in screen printing (especially using water based inks), our screens constantly come in contact with water, especially in.
